Concrete and paving glossary - C
A | B | C | D | E | F | G | H | I | J | K | L | M
N | O | P | Q | R | S | T | U | V | W | XYZ

Caisson
A 10" or 12" diameter hole drilled into the earth and embedded into
bedrock 3 to 4 feet. The structural support for a type of foundation
wall, porch, patio, monopost, or other structure. Two or more "sticks"
of reinforcing bars (rebar) are inserted into and run the full length
of the hole and then concrete is poured into the caisson hole. A caisson
is designed to rest on an underlying stratum of rock or satisfactory
soil and is used when unsatisfactory soil exists. See rebar
and pouring.
Calcite
The main raw material used in the manufacture of Portland cement. Calcite
is a crystallized form of calcium carbonate and is the principal component
in limestone, chalk, and marble.
Calcium aluminate cement
A combination of calcium carbonate and aluminates that have been thermally
fused or sintered and ground to make cement.
Calcium chloride
An additive used in ready-mix to accelerate the curing, usually used
during damp conditions. See ready-mixed
concrete.
Capillary space
A term used to describe air bubbles that have become embedded in cement
paste.
Cast-in-place concrete
Concrete that is poured into forms that are erected at the job site.
It is the same as the term sitecasting. See pre-cast
concrete.
Casting
Pouring a liquid material, or slurry, like concrete, into a mold or
form whose physical form it will take on as it solidifies. See pouring.
Casting bed
A permanent, fixed form, in which permanent pre-cast concrete forms
are produced. See pre-cast
concrete, cast-in-place concrete.
Cefi
A contraction meaning a cement finisher.
Cem. Fin.
The construction abbreviation for a cement finish.

Cement
A material composed of fine ground powders that hardens when mixed
with water. Cement is only one component of concrete. The gray powder
that is the "glue" in concrete.
Cement-aggregate ratio
The ratio of cement to aggregate in a mixture, as determined by weight
or volume.
Cement content / cement factor
A quantity of cement contained in a unit volume of concrete or mortar,
ordinarily expressed as pounds, barrels, or bags per cubic yard.
Cement mixer
A concrete mixer. A container used to mix concrete ingredients by means
of paddles or a rotary motion. The container may be manually or power-operated.
Cement mixtures
Mixtures are always listed as parts Cement to Sand to Aggregate. Following
are typical cement mixtures description:
-
Rich - 1 part cement, 2 parts sand, 3 parts coarse aggregate.
A rich mix is used for concrete roads and waterproof structures.
-
Standard - 1 part cement, 2 parts sand, 4 parts coarse aggregate.
A standard mix is used for reinforced work floors, roofs, columns,
arches, tanks, sewers, conduits, etc.
-
Medium - 1 part cement, 2 1/2 parts sand, 5 parts coarse
aggregate. A medium mix is used for foundations, walls, abutments,
piers, etc.
-
Lean - 1 part cement, 3 parts sand, 6 parts coarse aggregate.
A lean mix is used for all mass concrete work, large foundations,
backing for stone masonry, etc.
Cement slurry
A thin, watery cement mixture for pumping or for use as a wash over
a surface.
Cement types
-
Type I Normal - is a general purpose cement suitable for practically
all uses in residential construction but should not be used where
it will be in contact with high sulfate soils or be subject to excessive
temperatures during curing.
-
Type II Moderate - is used where precaution against moderate
sulfate attack is important, as in drainage structures where sulfate
concentrations in groundwater's are higher than normal.
-
Type III High Early Strength - is used when high strengths
are desired at very early periods, usually a week or less. It is used
when it is desirable to remove forms as soon as possible or to put
the concrete into service quickly.
-
Type IV Low Heat - is a special cement for use where the amount
and rate of heat generated during curing must be kept to a minimum.
The development of strength is slow and is intended in large masses
of concrete such as dams.
-
Type V Sulfate Resisting - is a special cement intended for
use only in construction exposed to severe sulfate action, such as
western states having soils of high alkali content.
Cementitious
Any material having cementing properties, usually referring to substances
like Portland cement and lime. See Portland
cement.
Central plant
A facility that makes and distributes ready-mix or pre-mixed concrete
loading the material into agitator trucks. See ready-mixed
concrete and agitator
trucks.

Chair
A small metal or plastic support for reinforcing steel in concrete
construction. The support is used to maintain proper positioning during
concrete placement. See bar
support/bar chair and high
chair.
Cinder block
A masonry block made of crushed cinders and Portland
cement. This type of block is lighter and has a higher insulating
value than concrete. Because moisture causes deterioration of cinder
block, it is used primarily for interior rather than exterior walls.
See concrete block.
Clinker
The resulting admixture from burning a combination of limestone with
silica, alumina, and iron oxide-containing materials. A lump or ball
of the fused material, usually 1/8" to 1" in diameter, is formed by
heating cement slurry in a kiln. Clinker, when cool, is ground into
a fine powder and interground with gypsum to form cement. See admixture.
Clip ties
Sharp, cut metal wires that protrude out of a concrete foundation wall
(that at one time held the foundation form panels in place).
Coarse aggregate
Naturally occurring, processed or manufactured, inorganic particles
in prescribed gradation or size range. The smallest size particle will
be retained on the No. 4 sieve.
Cold joint
A visible line that forms when the placement of concrete is delayed.
The concrete in place hardens prior to the next placement of concrete
against it.
Cold-rolled solid steel form
pins
Concrete
forming metal pins made from steel that has been rolled to its final
form at a temperature at which it is no longer plastic giving the pins
a dense, smooth, surface finish and high tensile strength. See hot-rolled
solid steel form pins.
Column clamp
A latching device for holding the sections of a concrete-column form
together while the concrete is being placed.
Column form
Specialized forms for creating low height columns typically used as
parking lot light anchors, communication tower bases, and similar applications
where short columns are required.
Compaction
The elimination of voids in construction materials, as in concrete,
plaster, or soil, by vibration, tamping, rolling, or some other method
or combination of methods. The process of eliminating voids in the non-set
concrete mixture that has been placed often using various vibration
devices. A sister operation to placing, compaction rates should be about
equal to the time it takes to place. See placing
and rodding.
Composite construction
Any element in which concrete and steel, other than reinforcing bars,
work as a single structural unit. See rebar.
Compressive strength
The ability of a structural material to withstands squeezing forces.
The maximum compressive stress which material, Portland cement, concrete,
or grout is capable of sustaining.
Concrete
Concrete is a hardened building material created by combining a mineral
(which is usually sand, gravel, or crushed stone) a binding agent (natural
or synthetic cement), chemical additives, and water. It is an excellent
material to be used in road building, bridges, airports, factories,
waterways and other construction projects. Concrete is the mixture of
Portland cement, sand, gravel, and water used to make garage and basement
floors, sidewalks, patios, foundation walls, etc. It is commonly reinforced
with steel rods (rebar) or wire screening (mesh). See binder,
cement, Portland
cement, and rebar.

Concrete block
A concrete masonry unit, most often hollow, that is larger than a brick.
See concrete masonry unit (CMU).
Concrete contraction
The shrinkage of concrete that occurs as it cures and dries. See shrinkage.
Concrete finish
A description of the smoothness, texture, or hardness of a concrete
surface. Floors are trowelled with steel blades to compress the surface
into a dense protective coat. See trowel,
troweling, and trowel
finish.
Concrete finishing machine
A portable machine with large paddles like fan blades used to float
and finish concrete floors and slabs. A large power-driven machine mounted
on wheels that ride on steel pavement forms. These machines are used
to finish concrete pavements. See float
and finishing.
Concrete masonry unit (CMU)
A block of hardened concrete, with or without hollow cores, designed
to be laid in the same manner as a brick or stone. A CMU is also referred
to as a concrete block. See concrete block.
Concrete mixture
The percentage of cement content contained in the concrete. A rich
mixture contains a high proportion of cement. A lean mixture is a mixture
of concrete or mortar with a relatively low cement content. A harsh
mixture of concrete is one without mortar or aggregate fines, resulting
in an undesirable consistency and workability. See aggregate,
cement, cement content/cement
factor, cement mixtures, cement
types.
Concrete transporting
The process of moving the concrete mixture from the central plant,
or mixing location, to the construction site. Transporting devices include
agitator trucks, buckets, wheelbarrows, conveyors, and pumping devices.
See agitator truck.
Connector bolts
(1) Fastening devices used to connect forms and forming accessories.
The typical style is a slotted bolt with a locking wedge so concrete
residue cannot form on standard bolt.
(2) Bolts designed with vertical slots used in conjunction with a small
metal wedge to attach two flatwork forms together during stacking use.
See flatwork forms,
flexible forms,
stacking, and straight
forms.
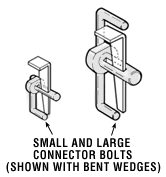
Consistency
The degree of plasticity of fresh concrete or mortar. The normal measure
of consistency is slump for concrete and flow for mortar. See slump
and slump test.
Consolidation
Compaction usually accomplished by vibration of newly placed concrete
to minimum practical volume, to mold it within form shapes and around
embedded parts and reinforcement, and to eliminate voids other than
entrained air.
Construction joint
The contact between the placed concrete and concrete surfaces, against
or upon which concrete is to be placed and to which new concrete is
to adhere, that has become so rigid that the new concrete cannot be
incorporated integrally by vibration with that previously placed. Unformed
construction joints are placed horizontally or nearly horizontally.
Contractor
A person or company licensed to perform certain types of construction
activities that undertakes a legal obligation to perform specified construction
work. Types of contractors include:
-
General contractor - responsible for the execution, supervision
and overall coordination of a project and may also perform some
of the individual construction tasks. Most general contractors are
not licensed to perform all specialty trades and must hire specialty
contractors for such tasks, e.g. electrical, plumbing.
-
Remodeling contractor - a general contractor who specializes
in remodeling work.
-
Specialty contractor - licensed to perform a specialty task
e.g. electrical, side sewer, asbestos abatement.
-
Sub contractor - a general or specialty contractor who works
for another general contractor.

Control joint
Tooled, straight grooves made on concrete floors to "control" where
the concrete should crack.
Corner forms
Metal concrete forms that are specialized forming accessories that
are attached to straight forms to form 90° corners. Typical applications
for corner forms include patios, sidewalks, warehouse floors, slab on
grade house foundations, and similar flatwork applications. See slab
on grade and straight
forms.
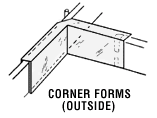
Cream
Construction slang term to describe the cement and sand component of
ready-mix that rises when the aggregate is worked down by way of agitation
floating, troweling, screeding, etc. This is also referred to
as "juice". See float, floating,
ready-mixed concrete,
screed, screeding,
trowel, and troweling.
Curb and gutter
The border area of a street, or other paved surface, that includes
a curb, an extruded or hand-formed berm, and a gutter, the area designed
to remove and transport water away from the main paved area. Both parts
are usually made out of concrete. See curb
and gutter combination and curb and
gutter forms.
Curb and gutter accessories
Forming components, specialized tools, and attachments that are used
to facilitate curb and gutter placement and include hangers,
bracing, stake
pullers, filler forms,
form stakes, form
pins, and curbface mules.
Curb and gutter combination
Refers to curbs and gutter combinations that are formed in the same
concrete pour. The curb portion varies from 4" to 12" in height and
is used to prevent vehicles from leaving a paved area. The gutter portion
varies from 6" to 12" in width and is used to control water runoff from
pavement. The elevation of the gutter is either slightly above, or slightly
below, the grade of the pavement. Additionally, the gutter itself will
have a slight inward or outward slant to direct the flow of water either
towards or away from the curb, dependent on the desired water flow.
See pouring, pitch-in,
and pitch-out.
Curb and gutter face forms
Metal forms used in placing concrete that attach to the curb and gutter
system to form the profile for the curbface.
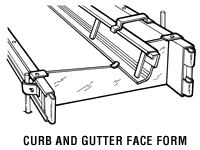
Curb and gutter forms
Concrete forms and accessories used to pour a curb and gutter combination.
The curb and gutter forming systems consists of a back form, a face
form, a front form, a division plate and a top spreader. Back and front
forms are standard straight forms with the back form taller than the
front form for a curb and gutter combination configuration. See division
plate, straight
forms, and top spreader.
Curbface batter
Curbface batter refers to the distance between the top slope of a
curbface and the bottom slope of a curbface. See batter.
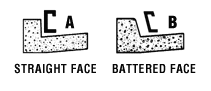
Curbface mule
A mechanical tool used to form the desired curb profile for any curb
and gutter application. See curb and gutter
forms.
Curbface tool
A hand tool made to match the profile of the curbface used to finish
and smooth the curbface after concrete placement, but before concrete
hardening. See mule.
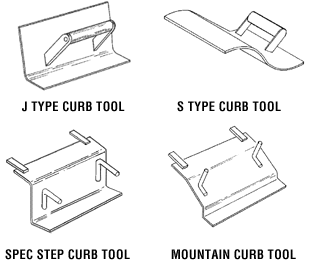
Curbface transition forms
Curbface transition forms allow a contractor to quickly change from
a straight to a radius curb and back to a straight curb. They usually
come in male/female pairs.
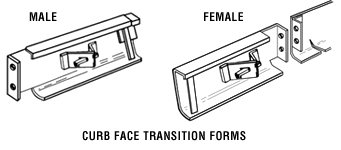
Cure
Method of maintaining sufficient internal humidity and proper temperature
for freshly placed concrete to assure proper hydration of the cement,
and proper hardening of the concrete. See hydration.
Curing
The hardening of concrete, plaster, or other wet material. Curing typically
occurs through the evaporation of water or a solvent, hydration, polymerization,
or chemical reactions of various types. It is the final process, after
placing and compacting, that ensures the concrete will set to its desired
strength. The length of time is dependent upon the type of cement, mix
proportion, required strength, size and shape of the concrete section,
weather and future exposure conditions. The period may be 3 weeks or
longer for lean concrete mixtures used in structures such as dams or
it may be only a few days for richer mixes. Favorable curing temperatures
range from 50° to 70° F. Design strength is achieved in 28 days.
See cement mixture, compaction,
hydration, and set.
The American Concrete Institute defines curing as maintaining satisfactory
moisture content and temperature in concrete during its early stages
so that it may obtain the desired properties. See placing
and compaction.
Curing blanket
A layer of straw, burlap, sawdust, or other suitable material placed
over fresh concrete and moistened to help maintain humidity and temperature
for proper hydration. See burlap,
curing, curing compound,
and curing membrane.
Curing compound
A chemical applied to the surface of fresh concrete to minimize the
loss of moisture during the first stages of setting and hardening. See
curing, curing membrane,
and curing blanket.
Curing membrane
Any of several kinds of sheet material or spray-on coatings used to
temporarily retard the evaporation of water from the exposed surface
of fresh concrete, thus ensuring a proper cure. See burlap,
curing, curing compound,
and curing blanket.
Custom forms
A variety of unique forms used for specialized concrete forming such
as reversible forms,
super flat forms,
tilt-up forms, tilt-up
reversible forms, foundation
set forms, seawall
forms, rehab forms,
and column forms.
Cut and fill
A term used to describe the addition or subtraction from a grade mark.
Also, an operation commonly used in road building and other rock and
earthmoving operations in which the material excavated and removed from
one location is used as fill material at another location.
A | B | C | D | E | F | G | H | I | J | K | L | M
N | O | P | Q | R | S | T | U | V | W | XYZ

|